- Home
- Blog
Universal crusher operation description
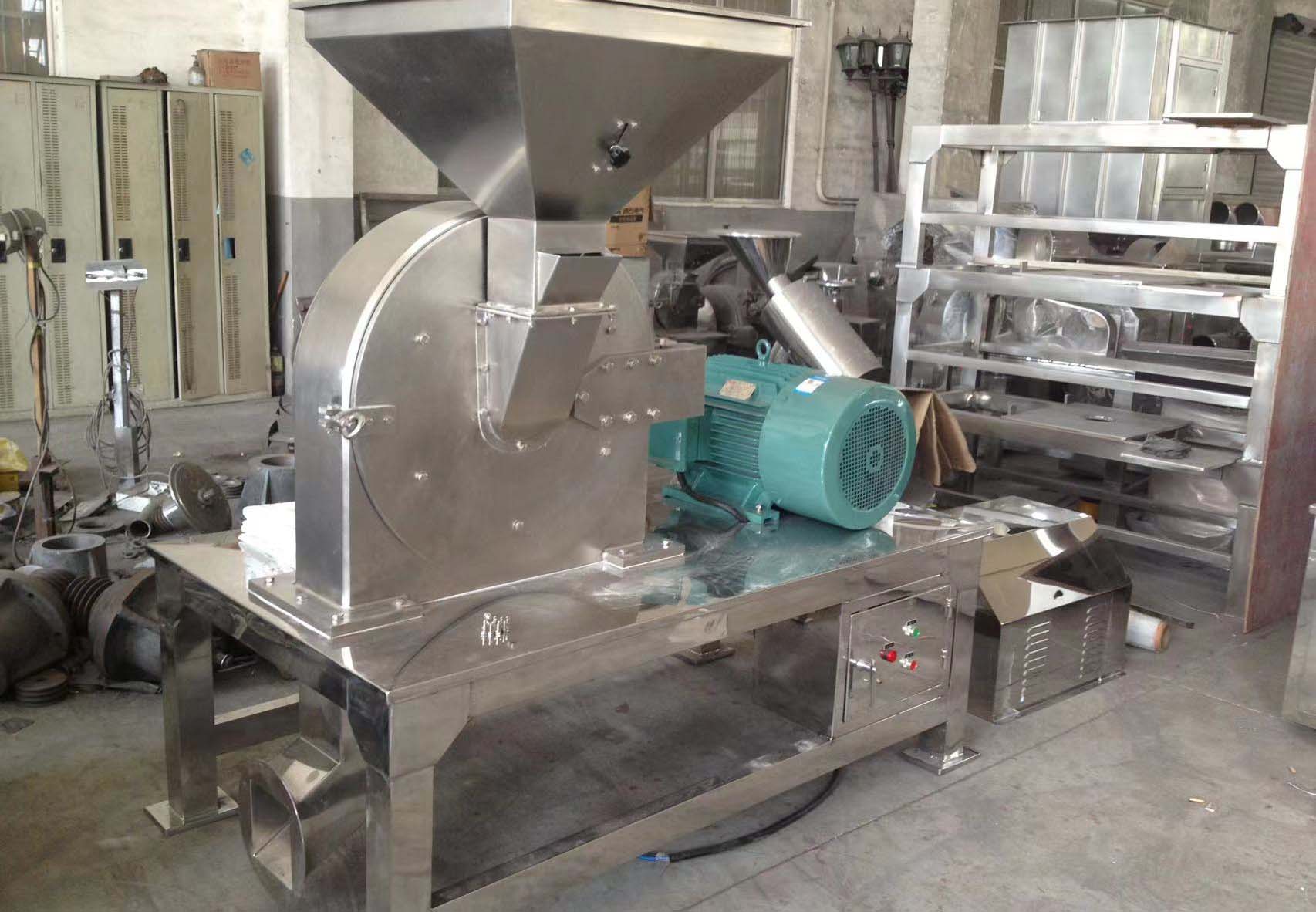
The function of the universal crusher is also very powerful. Compared with ordinary crushing machines, whether in terms of appearance and performance, universal crusher has superiority, fast processing speed, and can crush various materials. In addition, the universal crusher also breaks through the traditional limitations and turns some processing into possible.
It is best to stop the feeding before the device is stopped. In addition, it is necessary to regularly check whether the knife and screen network are damaged. If it is damaged, it should be replaced immediately. The direction of the main axis should be directed to the arrow shown on the protective cover, otherwise it will damage the machine and may cause personal damage.
Whether the electrical appliances are complete and the machine crushing the room must be checked clearly, because if there are hard miscellaneous objects, it will break the props and affect the operation of the machine. Of course, the material must be checked before crushing, and there is no mix of metal hard debris, so as not to hit the knife or cause accidents.
It should be reminded that the feeding speed of the universal crusher is too fast, the load increases, and it is easy to cause blockage. Therefore, in the process of feeding, pay attention to the large turn angle of the current meter pointer at any time. If the rated current exceeds the rated current, it indicates that the motor overloads and overloads for a long time, and the motor will be burned.
Before use, check whether all fasteners of the machine are tightened and the belt is tight.
- The direction of the main axis must meet the direction of the arrow shown on the protective cover, otherwise it will damage the machine and may cause personal damage.
- Check whether the electrical appliances are complete.
- Check whether there are hard debris such as metal in the machine crushing room, otherwise the knife will be broken to affect the operation of the machine.
- The material must be checked before crushing. The metal hard debris is not allowed to be mixed in order to avoid accidents or cause accidents.
- The oil cups on the machine should be injected frequently to ensure the normal operation of the machine.
- Stop the feeding before stopping.
- Regularly check whether the tool of the tool is damaged. If it is damaged, it should be replaced immediately.
- The use of the opportunity to experience a small vibration. Be sure to tighten the cover of the cover to avoid accidents.