- Home
- Blog
Air cooling vibrating screen for PVC granules
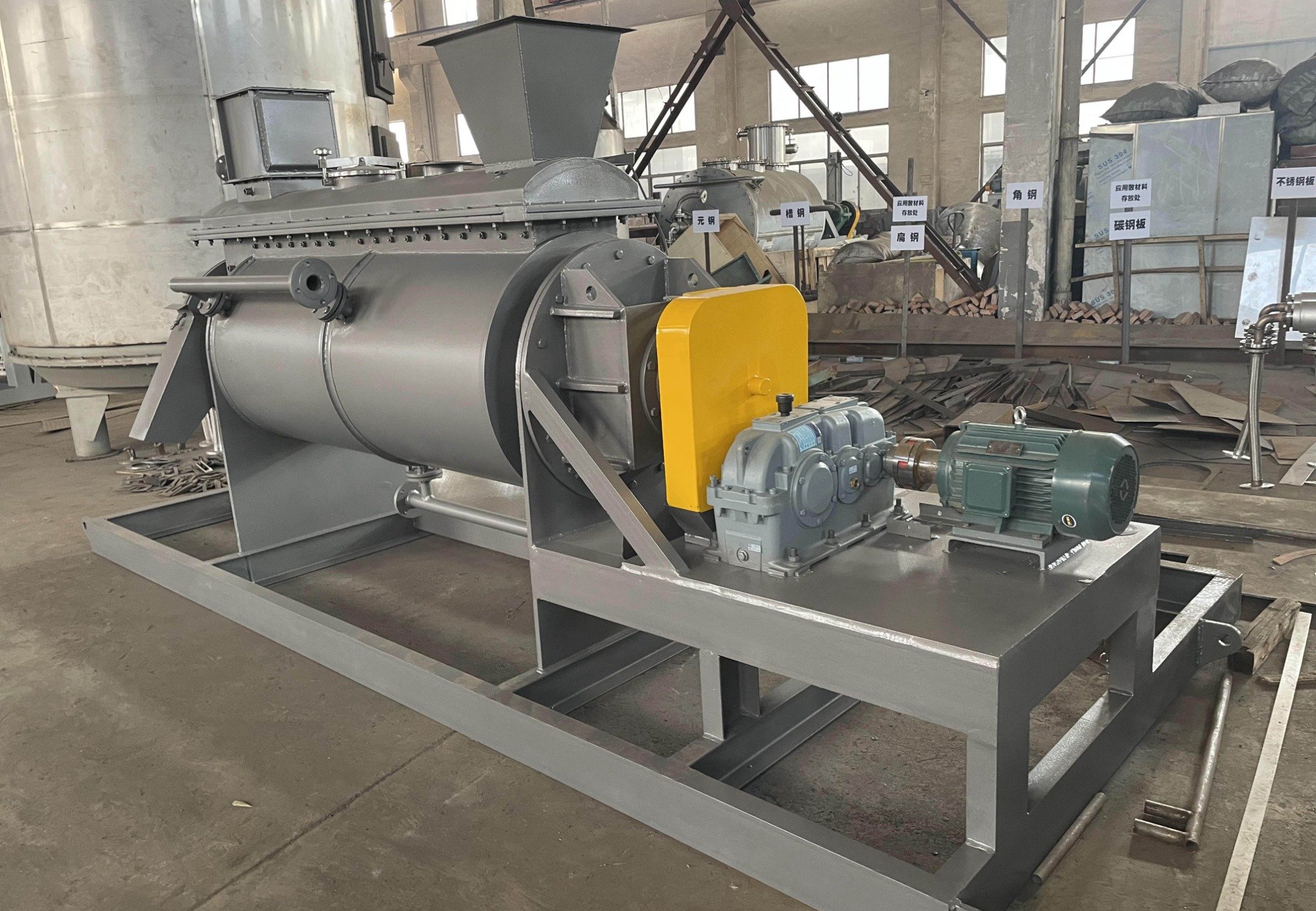
How Does Hollow Paddle Dryer Work?
Densely lined with wedge-shaped hollow shaft hollow blades, heat medium through the hollow axial flow through blades. Unit effective volume of a very large area of heat transfer, heat medium temperature from -40 to 320 ℃, can be water vapor, may also be liquid-type:such as water, oil and so on. Indirect conduction heating, the air does not carry away the heat, the heat are used to heat materials. Only through the device body heat loss to the environment, heat insulation layer. Wedge-shaped blades with self-cleaning heat transfer surfaces .
Wedge-shaped surface material particles and scrubbing effect relative movement, to wash away the wedge surface material attachments, so in operation have maintained a clean heat transfer surfaces. Blade dryer for the W-type shell, the shell of the general arrangements for 2-4hollow stirring shaft. Shell with a sealed cover with the cover to prevent dust leakage and collection of materials, solvent vapor materials. Set out and exit pull a block, to ensure a high degree of material level, so that heat transfer surface is covered with fully materials.Heat medium through the rotary joint, passing through the shell jacket and the hollow stirring shaft, hollow shaft stirring according to the type of thermal media have different internal structures to ensure the best heat transfer.
Hollow Paddle Dryer Features
1. Blade dryer energy consumption is low: as indirect heating, the air does not carry away a lot of heat insulation of dryer wall has, on the slurry material, evaporation of 1kg of water vapor only 1.22kg of steam.
2. Blade dryer system costs low: within the effective volume of units have a large heat transfer surface, the reduced processing time, equipment size becomes smaller . Would greatly reduce the building area and building space.
3. Dealing with a wide range of materials: using a different hot medium, able to deal with heat-sensitive materials can be heat-treated materials handling.Commonly used media are: water, steam, oil, hot water, cooling water. Continuous operation can also be intermittent operation can be applied in many fields.
4.Environmental pollution: do not carry air, dust entrainment few materials. Solvent evaporation of material is very small, easy to handle. To have contaminated materials or be recycled solvent conditions, can be used closed circuit.
5.Operation stability: As the wedge-shaped blades of special compression – expansion of stirring, so that material particles sufficient surface contact with the heat transfer in the axial zone, the material temperature, humidity, mixed density gradient is very small, thus ensuring the process stability.